An exploration of field coils and power supplies began some years ago. Loudspeaker magnet materials have evolved since the 1920s: field coil, Alnico, Ticonal, ceramic and rare earth materials - neodymium, samarium-cobalt, etc... .
All sound different. How they compare is beyond the scope of this post. The focus here is on various field coil supply types and how they affect the sound.
Battery was the original field coil supply while Tungar supplies were the battery chargers. Batteries wear out and Tungar eventually became the on hand, zero cost, battery replacement - more practical for theatres to use than lead/acid battery's, acid, distilled water and hydrometers. The highest seniority union projectionist in the USA recounted many things of this nature to me in North Texas during the middle 90's (long before I was interested in field coils) as we harvested derelict theatre gear in the dark with flashlights. He recounted pushing stacks of tube amps down stairs, banging basket ball sized mercury vapour rectifiers to initiate arc, film fires, drive-in tailgate parties and the demise of theatres, at the first drive-ins and then the grand marque theatres of cities and towns. My first RCA Ubangi and Altec VOT speakers came from spelunking with him into the darkened, abandoned theatres. Texas style heat, darkness, and the stench of pigeon guano mixed with eau de dead rat was the olfactory cocktail. He set me straight when I began to harvest some Tungar supplies and re-directed me toward the Altec drivers in VOT cabinets behind the screen.
At each step micro detail became more densely populated with increasingly clean edges and space. Textures were richer, the personality of performers more clear, more alive.
Everything was clearly audible, which raises the question of how much music is being lost in conventional loudspeaker design. We know that 95% of an amplifiers power goes up in heat at the voice coil, how much fidelity must be going with it? Here perhaps we can get a little back through high sensitivity and the stability of the magnetic field.
Near this time a commission was accepted for a pair of field coil Sfera Loudspeakers which created the inertia to develop a plasma based rectifier (Mercury or Xenon Vapour) supply.
These devices posses unique characteristics. The low voltage drop remains constant through current variations. When current changes the plasma bridge merely expands into, or withdraws from, the highly conductive vapour cloud instead of dragging current across a resistive element as most tube rectifiers do. As a result it is a very low impedance rectifier as well as an organic form of regulation. This could explain their uncanny, natural sound.
The chokes in the LCLC were then upgraded with better core material, lower DCR, more henrys as well as common mode configuration with two coils on same core. Again, all clearly audible: greater distinction and impact of instruments and voices. Since all this was coming through so clearly I thought it would be interesting to see how far it could be taken before contrast between changes diminished. Nano crystalline core inductors went into the LCLC - again clearly audible.
I would say these differences were very similar in scale to those in designing an amplifier with different tubes, parts and various versions of power supply. In fact, I propose that if there are hallucinogens in audio they may reside in the power supply of a field coil. Bear in mind 104db sensitive speakers display these changes more vividly than others...
From this I believe it is safe to conclude that current delivery/low impedance is critical in these supplies and the nature of the elements such as capacitor ESR, inductor core type and DCR are readily perceived.
More to follow...
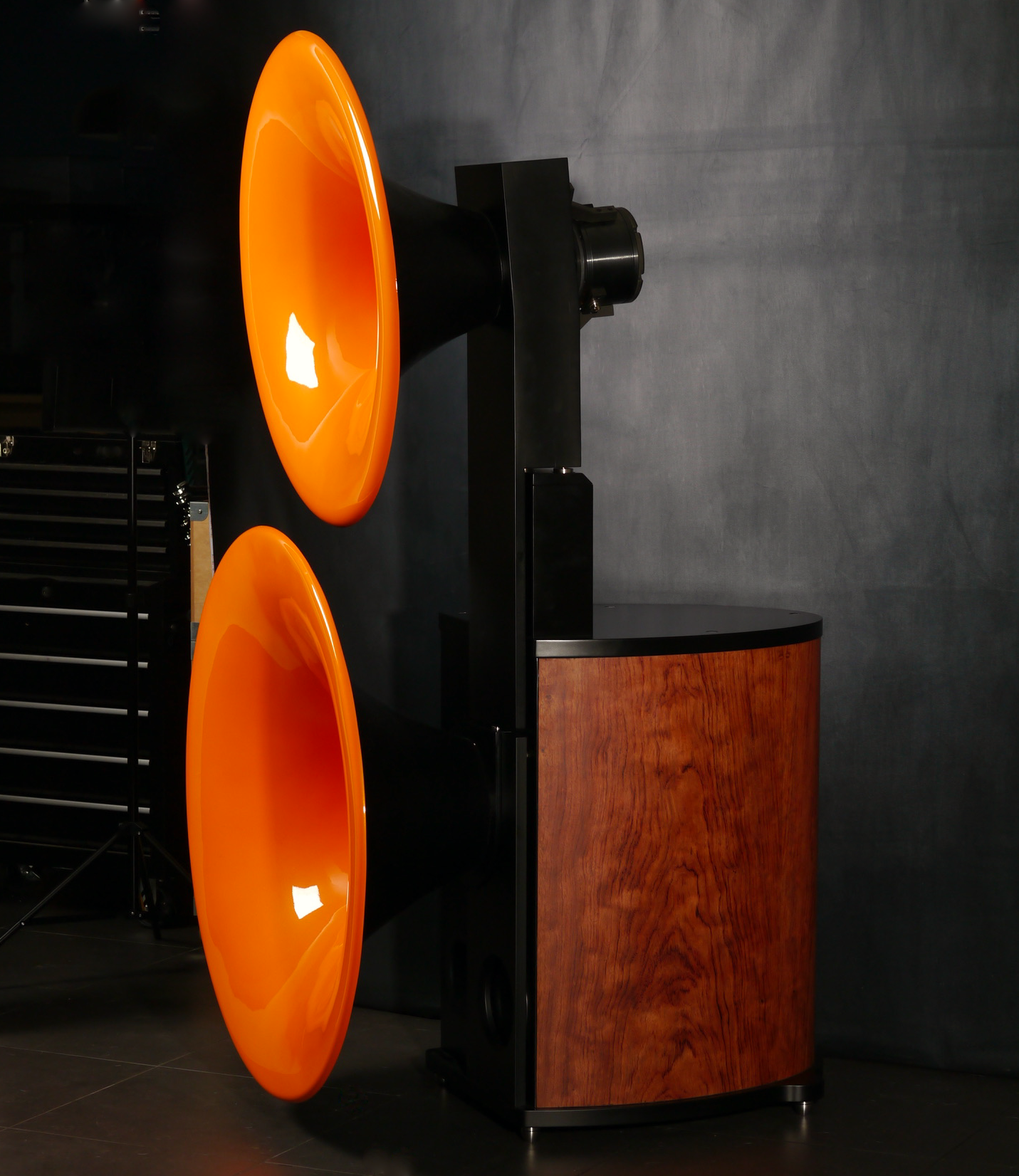